Graded polymer foams (GPFs) confer substantial mechanical stability in a lightweight form to various natural and technical materials. Their versatile properties are particularly sought after in applications such as energy absorption, insulation, or tissue engineering. For example, ideal bone mimics for tissue engineering recapitulate the solid skin as well as the density gradient towards its center in a way that allows cells and fluids to move freely within. GPFs can be produced using microfluidics (MFs), 3D printing or reaction injection molding. The resulting polymer foam properties can be tuned by using different polymers or by varying their morphology.
Foam templating using microfluidics allows one to adjust GPF parameters like the pore size, the degree of polydispersity and even the window size of the interconnection between pores with ease. Moreover, it can be scaled to liter per hour production rates [1-3]. However, attainable bubble sizes remain usually limited to roughly 100 – 1000 µm and only spherical structures can be produced. Costantini et al. [4] introduced a PDMS chip to formulate gradient foams (Figure 1 (left)) with controlled bubble sizes spanning one order of magnitude in real time. Conversely, additive manufacturing of GPFs using two-photon-polymerization (2PP) or stereolithography (SLA) offers tantalizing avenues. Fused filament deposition molding allowed Bates et al. [5] to create density gradient scaffolds of ~1 cm honeycombs (Figure 1 (right)). Improved energy absorption and damping profiles were observed for the graded honeycombs compared to their uniform counterparts. While freeform additive manufacturing usually covers extensive design space freedom, their sequential fabrication puts stringent limits on suitable fabrication volumes, especially for highest resolutions.
This work seeks to establish a combined microfluidic SLA 3D-printing approach for the synthesis of GPFs to combine the advantages of both techniques. For this purpose, ultracompact 3D microfluidic engineering [6] will be tailored for rapid foam production rates, increased bubble size ranges, as well as precise local foam property control. The morphology and the mechanical properties of the resulting GPFs are studied and compared. Our approach will expand the scope of designing innovative gradient and graded materials for tissue engineering, energy absorption, or insulation applications in the future.
[1] C. Stubenrauch et al., Angew. Chem. Int. Ed. 57 (2018), 10024 -10032. |
[2] S. Andrieux, A. Quell, C. Stubenrauch, W. Drenckhan, Adv. Colloid Interf. Sci., (2018), 256, 276-290. |
[3] F. Dehli et al., Journal of Colloid and Interface Science 588 (2021), 326-335. |
[4] M. Costantini, et al., Angew. Chem. Int. Ed. 58 (2019), 7620 -7625. |
[5] S. R.G. Bates et al., Materials and Design 162 (2019), 130-142. |
[6] J.L. Sanchez Noriega et al., Nat Commun 12 (2021), 5509. |
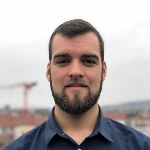
Oliver Walker
PhD Student

Cosima Stubenrauch
Prof. Dr.Dean of Faculty
- Profile page
- +49 711 685 64470
- Write e-mail
- Secretary: Room 9-302; Tel. +49 711 685-64451 and -64393; sekretariat2@ipc.uni-stuttgart.de